Gesucht: Ersatz für ein Multitalent
Luftig, billig, vielseitig: Lange war Styropor ein Lieblingsmaterial der Industrie. Nachteile für Umwelt und Gesundheit – geschenkt. Das hat sich geändert. Inzwischen gibt es für jeden Anwendungsfall ökologischere Alternativen. Was taugen sie – und wann werden sie den Plastikschaum verdrängt haben?
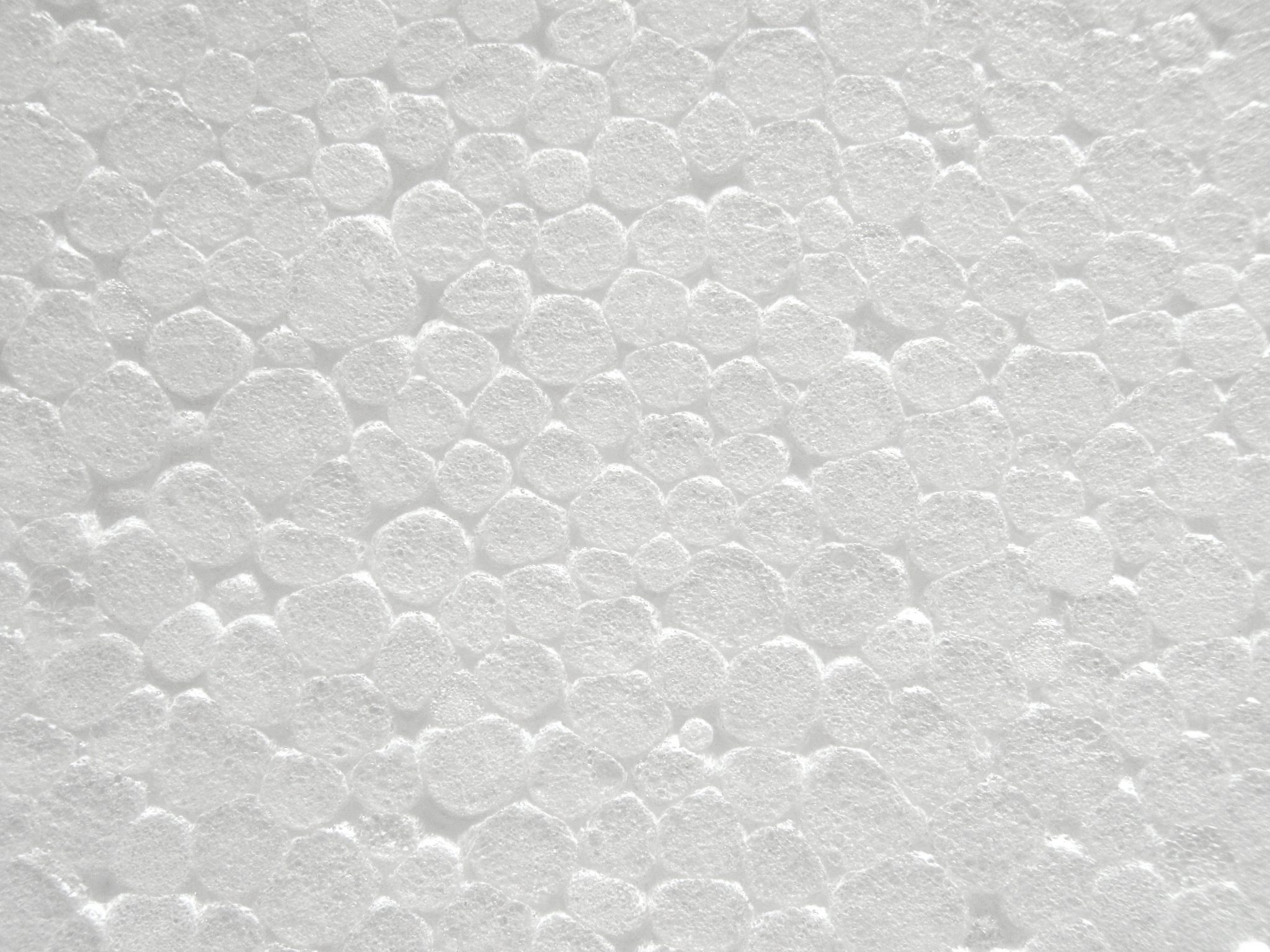
Zugegeben, das Material macht es der Konkurrenz nicht leicht. Der Erfolg von expandiertem Polystyrol (EPS), besser bekannt unter dem Markennamen Styropor, verdankt sich schließlich seinen vielen ausgesprochen praktischen Eigenschaften: Der aufgeschäumte Kunststoff ist superleicht, billig in jeder beliebigen Form herzustellen, dämpft Stöße hervorragend ab und besitzt die Fähigkeit, Kaltes kalt und Heißes heiß zu halten.
Allerdings steht auf der Negativseite eine mindestens ebenso beeindruckende Liste. EPS wird viel zu selten recycelt, weil schon das riesige Volumen des Schaumstoffs den Transport zu geeigneten Anlagen enorm teuer macht. Dafür gelangt er nur allzu leicht in die Umwelt, weil Verpackungen »fliegen gehen«. Dort zerbröseln sie im Lauf der Zeit, ohne aber zu verrotten. Die kleinen Kunststoffkügelchen wirken auf Fische, Vögel und andere Lebewesen wie Futter – ein fataler Irrtum. So richtig gesund ist EPS übrigens auch für uns Menschen nicht, denn aus Polystyrol löst sich immer wieder das hochgiftige Styrol. Außerdem wird dem Grundmaterial meist noch ein ganzer Chemiecocktail zugesetzt, um bestimmte Eigenschaften zu erreichen, und viele dieser Stoffe werden zumindest in Spuren auf den Verpackungsinhalt übertragen.
»Es gibt heute im Bereich Verpackung keinen Grund mehr, EPS einzusetzen. Und tatsächlich ist der Einsatz drastisch zurückgegangen.« – Chemiker Michael Braungart, Gründer des Hamburger EPEA-Insituts.
Weg vom weißen Schaum
»Es gibt heute im Bereich Verpackung keinen Grund mehr, EPS einzusetzen«, erklärt Chemiker Michael Braungart, der als Gründer des Hamburger EPEA-Instituts Unternehmen bei der Entwicklung umweltfreundlicher Produkte und Materialien berät. »Und tatsächlich ist der Einsatz drastisch zurückgegangen.«
Stimmt. Beim Nachdenken fällt auf, dass sich in den letzten Jahren einiges verändert hat. Äpfel liegen jetzt in Papp- statt Styroporschalen (allerdings allzu oft immer noch unter Plastikfolie), weiße Schaumstoffbecher sind aus der hiesigen Coffee-to-go-Kultur verschwunden, und selbst die Fast-Food-Riesen stecken ihre Burger inzwischen in Pappboxen. Aber der neu gekaufte Bildschirm liegt im Karton immer noch in einer schützenden Umhüllung aus EPS, das Gleiche gilt für andere Elektro- und Elektronikprodukte – und nicht nur die. Geht das auch anders?
Kunststoffschaum auf Biobasis
Es geht. Die naheliegendste Alternative ist schlicht ein anderer geschäumter Kunststoff, aber einer auf Basis von nachwachsenden Rohstoffen. Im Fall von BioFoam, hergestellt von der niederländischen Firma Synbra, sind das Stärke und Zuckerrohr, aus denen Biopolymere auf Basis von Milchsäure gewonnen werden. Das Endprodukt sieht EPS täuschend ähnlich (wird zur besseren Unterscheidung aber grün eingefärbt) und besitzt ähnliche Eigenschaften. Der entscheidende Unterschied: Es kann wieder zu Nährstoff für Pflanzen werden – jedenfalls theoretisch, wenn es in eine leistungsfähige industrielle Kompostierungsanlage gelangt. Und das wiederum setzt voraus, dass es nicht doch fälschlich im Kunststoffmüll landet, wie es bei Biokunststoffen leider oft passiert.
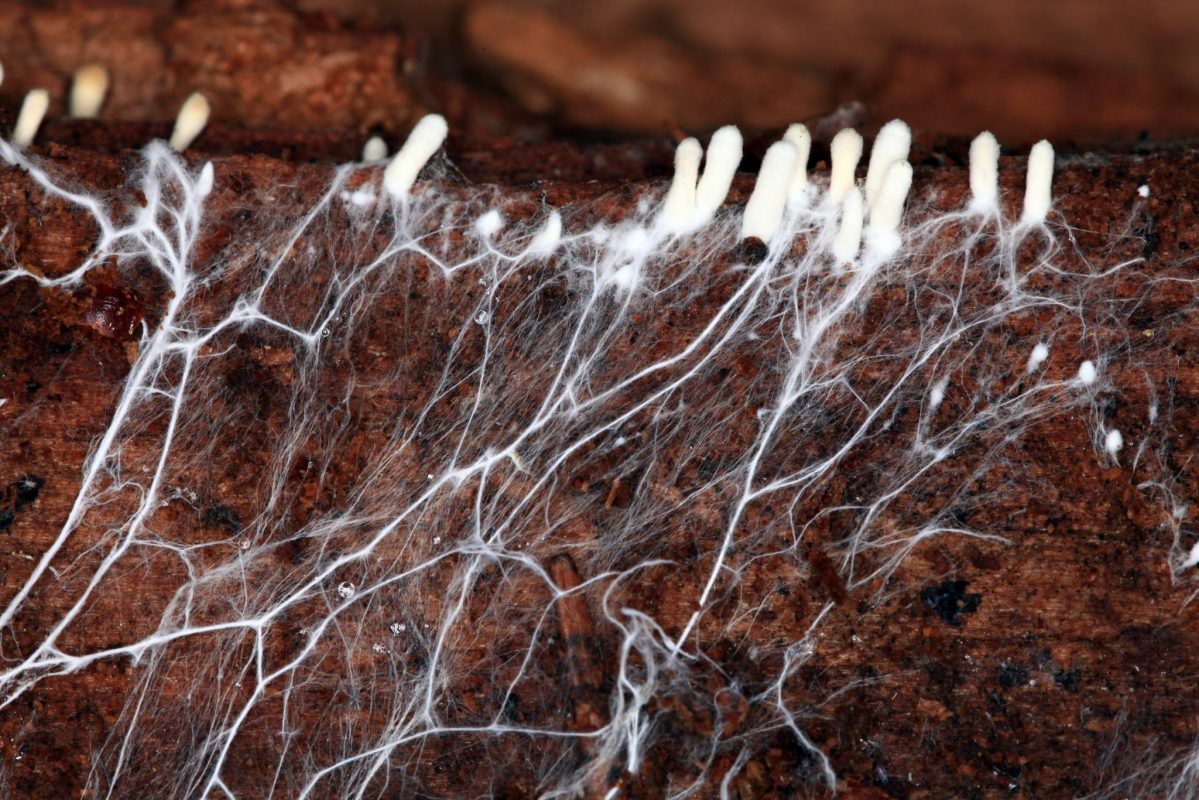
Leicht, formstabil, nachwachsend: Material auf Pilzbasis
Diese Gefahr dürfte bei dem Material, das die Gründer des New Yorker Start-ups Ecovative entwickelt haben, eher gering sein. Nach Plastik sieht hier nichts aus. Nach Pilzen allerdings auch nicht, aber genau darum handelt es sich. Nicht um die Fruchtkörper allerdings, sondern um das Myzel, also den eigentlichen Pilzorganismus.
Er wächst um ein Substrat aus landwirtschaftlichen Abfällen herum. Maisblätter, Reishülsen oder Baumwollsamenkapseln werden dazu in eine Form gefüllt. Sobald der Pilz diesen Nährboden mit seinen feinen Myzelfäden vollkommen durchzogen hat, wird die Masse erhitzt und damit getrocknet. So entsteht ein sehr leichtes, stabiles Material mit sehr guten Dämmeigenschaften, das sich in beliebigen Formen züchten lässt. Hat es seinen Zweck erfüllt, kann es zudem einfach kompostiert werden – und zwar ohne industrielle Anlage, einfach im eigenen Garten. Ecovative listet bekannte Firmen wie Dell oder Ikea als KundInnen auf. Im deutschsprachigen Raum wird der Pilzschaumstoff allerdings bisher nicht in Computer- oder Möbelverpackungen eingesetzt. Es ist zu hoffen, dass die Pilztechnologie bald auch in Europa aufgegriffen wird.
Traditionelles Material wiederentdeckt
Während die Verwendung von Pilzmyzel einiges an Entwicklungsarbeit erfordert, kommen andere Styroporalternativen ziemlich low-tech, aber deshalb nicht weniger effektiv daher: Die Firma Landpack verarbeitet Stroh oder Hanf, gepresst oder lose in Hanfvliese gefüllt, zu isolierenden und stoßdämpfenden Packelementen. Arne Bläsing, Geschäftsführer des Fleischversenders Elbwild, berichtet von seinen Erfahrungen damit: »Ich wollte von Anfang an eine Verpackung, die nachhaltig ist und damit zu meinem Unternehmen passt. Bei meinen Kunden kommt das gut an. Und selbst das Veterinäramt war begeistert, denn die Kühlkette wird nicht unterbrochen. Die Kältewerte sind ähnlich wie bei Styropor.« Die Packelemente nimmt er wieder zurück, um sie mehrfach zu verwenden. Zum Schluss kann das Stroh mitsamt Hanfvlies einfach kompostiert werden.
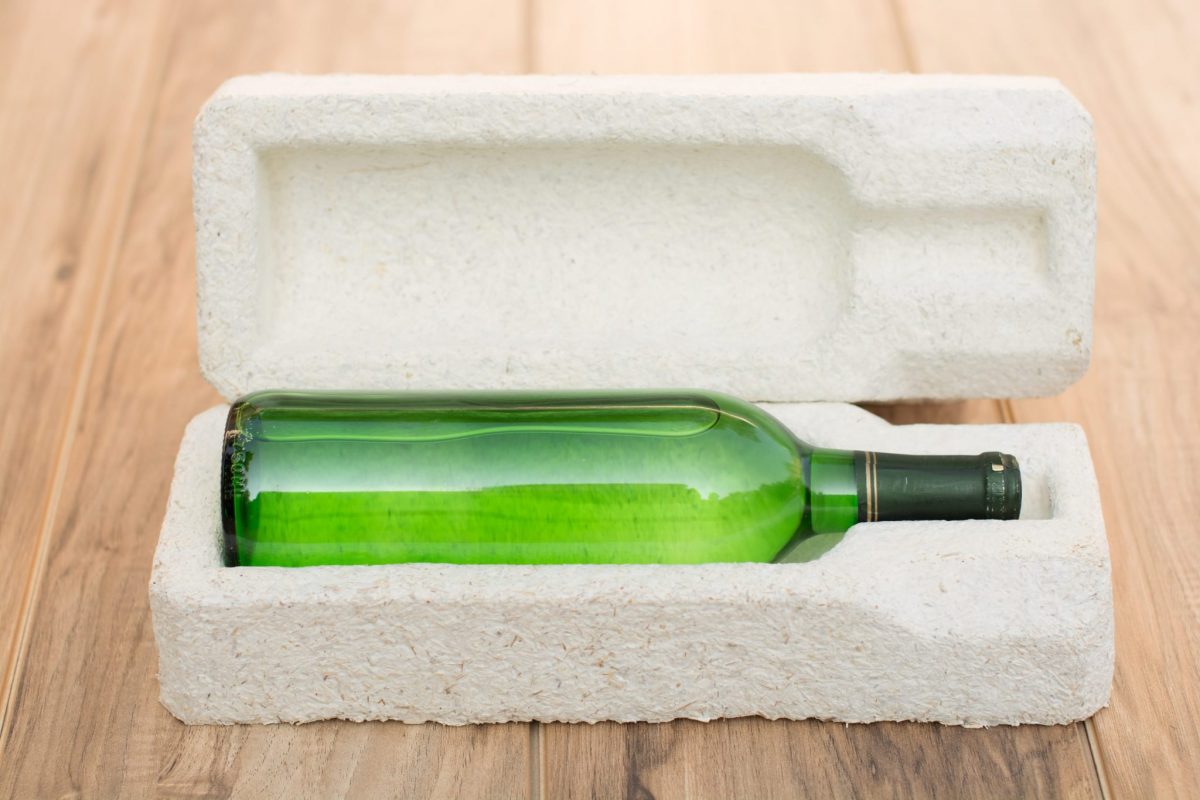
Multitalent Karton
Doch für die meisten Anwendungen bietet sich als EPS-Ersatz ein alter Bekannter an: Karton. Immer raffinierter werden die Faltungen, Aussparungen und Einsätze in Transportkartons, immer effektiver beim Abfangen von Stößen auch für empfindliche Güter. Für andere Anwendungen kann Papiermasse sogar in Form gespritzt oder aufgeschäumt werden. Und das Recycling von Pappe und Papier ist Routine; angefangen bei der gut eingeübten Mülltrennung durch die VerbraucherInnen.
Leider finden sich allerdings in Recyclingpapier und -karton zunehmende Konzentrationen giftiger Druckfarben und Papierbeschichtungen, die Kartonverpackungen für Lebensmittel zum Gesundheitsrisiko werden lassen. »Das passiert, wenn man die Produktentwicklung nicht vom Ende her denkt«, konstatiert Braungart, der seit über dreißig Jahren daran forscht, wie sich Materialien so in immerwährenden Nutzungskreisläufen führen lassen, dass weder Umwelt noch Menschen Schaden nehmen – ja, dass beide sogar einen Nutzen davon haben.
»Außerdem gilt auch hier: Never change a running system. Jede Umstellung kostet Geld und bedeutet Aufwand, zum Beispiel für neue Maschinen oder größere Umverpackungen, von höheren Kosten für das Material einmal abgesehen.« – Kim Check, Geschäftsführerin des Deutschen Verpackungsinstituts
Beispiele gibt es genug – auch in Sachen EPS-Alternativen. Braungart gerät fast ins Schwärmen, als er aufzählt: Statt als Füllmaterial die früher üblichen Styroporflocken zu verwenden, können aufgepoppte Maischips erst empfindliche Waren schützen. Werden sie nach Gebrauch als Hühner- oder Schweinefutter verwertet, werden die produzierten Kalorien sogar sinnvoll eingesetzt. Eine andere Idee sind Vliese, die erst empfindliche Elektronik beim Transport schützen und danach als Mulchvliese in der Landwirtschaft Pflanzen vor Unkraut und Böden vor dem Austrocknen schützen, um schließlich untergepflügt zu werden und sich zu zersetzen.
Reichlich Alternativen – in der Theorie
Manche dieser EPS-Alternativen mögen noch exotisch wirken. Aber fest steht: Die Ideen sind da, die Technologie ebenfalls, und die Veränderungen kommen ins Rollen. Fragt sich also, warum immer noch so viele Firmen aufgeschäumtes Polystyrol in Verpackungen einsetzen. »Das Material ist einfach zu verarbeiten, leicht, kostengünstig, und es erfüllt die benötigten Anforderungen, beispielsweise im Hinblick auf die gewünschte Isolierwirkung oder die Resistenz gegen Feuchtigkeit«, erklärt Kim Cheng, Geschäftsführerin des Deutschen Verpackungsinstituts e. V. (dvi), einer Lobbyorganisation der Verpackungswirtschaft. »Außerdem gilt auch hier: Never change a running system. Denn jede Umstellung kostet Geld und bedeutet Aufwand, zum Beispiel für neue Maschinen oder größere Umverpackungen, von den höheren Kosten für das Material selbst einmal abgesehen. In den meisten Fällen wollen aber weder die Unternehmen noch die VerbraucherInnen mehr zahlen.«
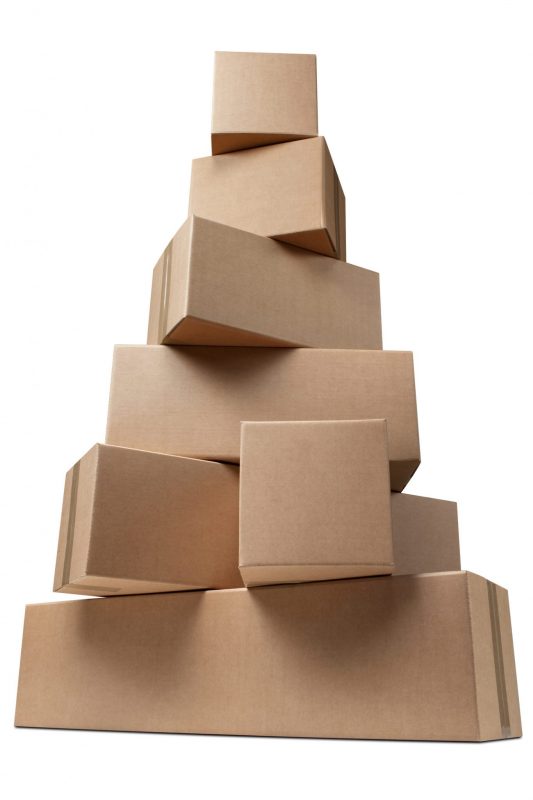
Die Kosten also. Liegt da der unüberwindliche Knackpunkt? EPS ist ja vor allem deshalb so billig, weil die Produktionsprozesse über Jahrzehnte hinweg optimiert wurden und weil das Material – auch für die Wärmedämmung – in so großer Menge hergestellt wird. Je stärker die Alternativen nachgefragt werden, desto effizienter dürfte auch ihre Herstellung werden. Bleibt also, für eine größere Nachfrage zu sorgen. Ein Anfang wäre es, wenn VerbraucherInnen gegenüber Handel und Industrie deutlich machten, dass sie es zu schätzen wissen, wenn ihre Produkte mit giftfreien, nachhaltigen Materialien verpackt werden.